For any concrete placement larger than 4 feet across in any dimension, project specifications typically require temperature monitoring of the concrete in several locations (core, face, etc.). There are usually restrictions placed on how high the temperature can be allowed to go, and also on how much the core temperature can differ from the outside edges (the “differential”). For example, most mass concreting specifications call for an absolute maximum temperature value of not more than 160°F, and a core-to-face differential of never more than 35°F.
The main reason for this degree of control is to reduce or eliminate cracking that can occur when the concrete gets too hot and the differentials are too great. It is especially important when the massive concrete is being used for things such as containment vessels or bridge piers, where even a single crack could require that the concrete be removed and replaced. From this, it is clear that accurate monitoring of temperatures in real time can be a vitally important means of staying in compliance of code requirements.
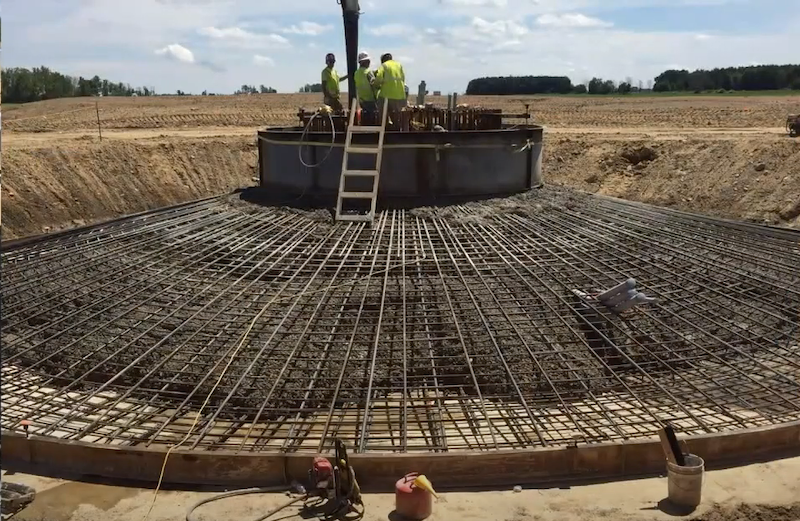
There are many methods of making sure that the massive concrete stays within spec, including:
- Optimizing the use of supplementary cementitious materials (SCMs) such as slag and fly ash in the concrete mix to keep the cement’s “heat of hydration” reaction under control, thus greatly reducing the peak temperatures.
- Insulating the entirety of the formwork to keep all of the concrete “warm” thus reducing the possibility that the differentials will go too high.
- Utilizing the maturity method to track interior concrete strengths which then allows the temperature differentials to be increased as the concrete is better and better able to tolerate such high differentials without detrimental effects. For example, one job eventually allowed a peak differential of 55°F after only 3 days because the interior concrete strength was so high, thus allowing the contractor to strip forms more than a week sooner than typically required.
- Running pipes throughout the mass and pumping coolant through the mass until the core temperatures and differentials are controlled naturally, usually 7-10 days. (This method is very costly and is falling out of favor very rapidly because of advancements in mix design optimization and maturity utilization.)
Today, there are many ways to monitor concrete temperatures, but Con-Cure NEX provides an easy way to keep the entire construction team informed about them in real-time. With each node able to monitor 3 locations within a single massive casting, even the largest mass can be monitored easily and thoroughly. The software also sends alerts for high temperature and high differential values. For example, the user can ask to be alerted when the concrete reaches a moderate temperature (say, 130°F) and then every 5 or 10 degrees thereafter, thus keeping everyone apprised of the progression.
Coupling simple temperature monitoring with maturity provides the entire construction team with the data they need to build quickly, while also ensuring compliance and peace of mind.